Technical Specifications
LP Separators
Low Pressure separators are tertiary separation devices used after primary segregation of the three phases i.e. Oil, Water and Gas from the initial inlet stream coming outside the Oil Wells and moving to the low-pressure separators before ending up in the stock tank.
Low pressure is necessary for the effective separation of lighter components in the liquid phase and making sure the water is made as pure as possible to be environmentally friendly. However, the low pressure must also be maintained at the optimum level so that it does not cause the lighter component in the liquid phase end to stabilize and the liquid-liquid separation is less efficient with a high liquid carryover in the outlet gas stream.
The LP separators have a similar configuration to that of the HP separators and can be manufactured tailor-made to the process requirements of the project.
HP Separators
High Pressure separators are primary separation devices used for segregation of the three phases i.e. Oil, Water and Gas from the initial inlet stream coming outside the Oil Wells and moving to medium and low pressure separators before ending up in the stock tank.
High pressure is necessary for the lighter components in the liquid phase to stabilize therefore resulting in quicker retention time and separation of liquids from each other. However, the high pressure must also be maintained at the optimum level so that it does not cause the lighter component in the liquid phase end up in the outlet gas stream.
Three-phase Separator
Three-phase separators are used in the segregation of the three phases of the inlet stream namely Oil, water and gas.
A three-phase separator has the following blueprint for the effective separation of three phases.
An Inlet deflector is used to lessen the inlet stream momentum and aid in the separation of gas from the liquid phase quickly. There are two perforated baffles or wave breakers to nullify the possibility of the creating waves in the vessel. This helps in making sure that the gas distribution is uniform and the liquid-liquid separation is efficient. The presence of weir plates make sure that the levels of oil and water is maintained such that the liquids gets separated and drawn at the respective sumps by the respective control valves. The mist extractor is placed at the outlet gas nozzle to coalesce the fine droplets interspersed in the gas and gets entrained in the liquid phase of the separator.
An Inlet deflector can be in the form of a deflector baffle, cyclone inlet, wave breakers, de-foaming plates and Vane type inlet device for high momentum. The weir plates are placed at the bottom of the vessel with the perforated baffles placed at optimum distances to ensure maximum separation occurs in the quickest time. The outlet mist extractor can be in the form of wire mesh demisters, or vane type demisters and are also available in cyclones.
The separators are available in horizontal and vertical vessel configurations, where the horizontal three-phase separator is ideal for Gas Handling, needing more space and easierto service, while the vertical three-phase separator is ideal for solids handling, needs less space and harder to service.
QWP offers manufacture and supply of vessels with internals including initial design for FEED stage evaluation, rating of existing designs and de-bottlenecking existing vessels. The detailed information for the services offered by QWP is available in the following pages.
Three-Phase Separator Internals – Vane Type Inlet Device
QWP make Vane Type Inlet Devices are ideal for reducing the momentum of the onrushing inlet stream and aids in the uniform distribution of the inlet stream. It is normally used for momentum of inlet fluids of 2100 Pa to 8000 Pa. The material grade will be usually in the stainless-steel grades to perform better against corrosion than that of carbon steel. The inlet device is made to the specific inlet nozzle size and vessel diameter
Three-phase Separator
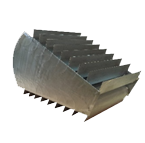
Three-phase separators are used in the segregation of the three phases of the inlet stream namely Oil, water and gas.
Features
- Specifically designed catching rims to capture additional liquid and minimize re-entrainment.
- Each row of vanes in the inlet device is welded to a mounting strip at the top and bottom.
- This device comes up with a vane ladder assembly.
- Ideal for Vessel sizes more than 500mm ID
- Better efficiency than half-open pipes
Three-Phase Separator Internals – Perforated/Calming Baffles
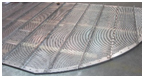
Perforated Baffles or Calming Baffles are used in the next stage of the gravity separation process in three phase separators. This internal is designed for even distribution just before the liquid-liquid separation region. This is paramount because, more the stable liquid phase, quicker is the retention time which is necessary for proper liquid-liquid separation. Double Perforated Baffle assembly is necessary for a three-phase separator while a single perforated baffle is sufficient for a two-phase separator.
Features
- Minimal Pressure drop
- Aids in even gas distribution
- Increase liquid-liquid separation efficiency
Three-Phase Separator Internals – Weir Plates/ Wave Breakers
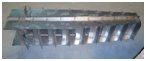
Weir plates or Wave breakers are plain plates placed right after a perforated baffle or a perforated baffle assembly. Its purpose is to synchronize the levels of the lighter components i.e. Oil and the heavier component i.e. Water in the liquid phase and aid in the liquid transfer to the respective liquid surge tanks/sump.
Features
- Paramount for maintaining levels of oil and water through control valves
- Simple and Efficient design
- One-time installation
Three-Phase Separator Internals – Mesh/Vane/CycloneMist Extractor
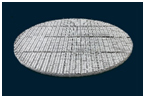
Mist Extractors are placed near the outlet gas nozzle that is placed on top of the vessel for the separation of gas. The mist extractor is required to coalesce the fine droplets entrained in the gas. The choice of mist extractor is to be arrived at after taking into consideration the e flow rate of the inlet stream.
Features
- Mesh Type Mist Extractor has the highest separation efficiency for droplets upto size 3μm but cannot withstand higher K factor
- Vane Type Mist Extractor has a better performance than the Mesh type Mist extractor in terms of handling high K factor while separation efficiency is ideal only for 15 microns onwards
- Cyclone Type Mist Extractor has the highest capacity for high factor but is relatively expensive to construct.
Three-Phase Separator Internals – Structured Packing/Coalescers
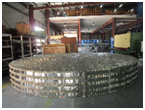
Coalescers are effective phase internals that are utilized for the liquid-liquid separation.
Features
- Low Pressure drop
- High Efficiency
- Low Liquid hold-up
Datasheets & Process Details
QWP offers customized process solutions with regard to the specific requirements of each project.
Features
- Inlet pipe sizing with taking into consideration of momentum and load calculation for inlet stream into vane type distributor
- Inlet piping flow regime maps
- Residence time calculations of different liquid levels
- Performance comparison between different inlet devices, outlet mist extractors, spacing of baffles etc.
- etailed separation parameter analysis such as K-Value, Gas velocity, Carryover etc.
- Vessel weight calculation, de-bottlenecking, optimum nozzle locating, optimum internals positioning and other specific parameters of vessel design.
- Easy-to-comprehend information by exhaustive graphs and charts